El mundo de la electrónica se expande constantemente. Las placas de circuitos PCB van cambiando según el uso en los dispositivos que se van creando. Podemos encontrarla en distintos dispositivos caseros, automotrices, industriales, militares, entre otros. Una leve falta de protección conduciría a un rendimiento reducido, posibles fallas notables o hasta una falla completa o total.
La protección que se puede puede proveer a estos, en su recubrimiento, están conformados generalmente de resinas de encapsulación o encapsulamiento.
Indice
¿Qué es mejor para proteger mi PCB, un recubrimiento o una resina?
Como en todo caso de ingeniería, depende del grado de protección ambiental requerido. Lo primero que se debe tener en cuenta, es el diseño de cualquier carcasa dentro de la cual se encerrará el PCB. Si un conjunto está encerrado en una carcasa que está diseñada para ser la protección ambiental principal, entonces a menudo se utiliza un revestimiento de conformidad para proporcionar un respaldo a la protección primaria proporcionada por la carcasa.
En los casos en que la carcasa no sea la adecuada o no pueda proporcionar la protección principal del conjunto contra su entorno de funcionamiento, la mayoría de las veces una resina podría ser la mejor opción.
¿Qué es un revestimiento y una resina?
Si notamos a ambos elementos, podemos considerar lo que es común entre los dos, ambos son generalmente polímeros orgánicos, que pueden emplearse para formar una capa eléctricamente aislante que proporcionan algún tipo de resistencia química o térmica. Hay un grado de coincidencia en la química de los polímeros utilizados, siendo el poliuretano, acrílico, silicona y el epoxi los más utilizados.
Resinas de encapsulación
Las resinas de encapsulación, otorgan el mayor nivel de protección para los PCB. Estas resinas pueden aplicarse desde un grosor de 0,5 milímetros, y generalmente se aplican con un grosor mucho mayor. El aumento del grosor conlleva un aumento significativo del peso y generalmente resulta en un precio unitario mayor que el de un revestimiento.
En esta situación, el aumento del espesor significa que el PCB está mucho mejor protegido contra el ataque químico, especialmente en los casos de inmersión prolongada. Además, una resina puede proporcionar una protección superior contra los choques físicos (dependiendo de la formulación), ya que el grueso de la resina ayudará a disipar las fuerzas a través del PCB, en lugar de permitir que se concentren.
Una capa de resina de color oscuro puede ocultar completamente el PCB, lo que permite una cierta seguridad en el diseño, y según la elección de la resina, la eliminación de esta, puede resultar en la destrucción del PCB.
Al encapsular toda la PCB, la resina proporciona un aislamiento integral de la unidad, combinando así buenas propiedades eléctricas con una excelente protección mecánica.
La protección mecánica puede identificarse de varias maneras: Se identifica la protección mejorada para las aplicaciones que implican una exposición prolongada o la inmersión en sustancias químicas fuertes, o las expuestas a choques vibratorios, físicos o térmicos, etc.
El nivel más alto de protección se logra a través de la masa y el espesor de la resina que rodea la unidad.
Las resinas, son generalmente sistemas de dos componentes, en los que una parte de esta, se mezcla con la cantidad correcta de endurecedor (Parte B), lo que inicia una reacción química que conduce a un polímero reticulado. Las resinas generalmente tienen una viscosidad mucho más alta, en comparación con un revestimiento, y a menudo contienen rellenos minerales para ayudar a su rendimiento.
Dado que no es necesario aplicar resinas por pulverización, en general las formulaciones de resina están libres de COV y la mayoría están diseñadas para curarse a temperatura ambiente. Sin embargo, el tiempo de curado puede reducirse mediante la aplicación de calor y, en el caso de algunas resinas, podría ser necesario un postcurado para que la resina desarrolle sus propiedades óptimas.
La mayoría de las resinas comenzarán a reaccionar tan pronto como los dos componentes se mezclen. La mayoría de las reacciones de curado son exotérmicas, ya que los enlaces químicos se rompen y se reorganizan.
La naturaleza de las reacciones exotérmicas es que se calienten, pero este calor puede controlarse mediante la selección del tipo de resina y un juicio cuidadoso de la cantidad de material que debe fundirse en un solo proceso, así como el diseño tanto del PCB como de la carcasa.
Si se aplica demasiada resina de una sola vez, los componentes pueden recalentarse, o incluso en el peor de los casos, la fundición puede incendiarse.
Debido a las variaciones en la aplicación, es vital que toda la unidad terminada sea probada en un entorno apropiado para su uso final previsto; puede tratarse de condiciones exactas o de pruebas aceleradas cuidadosamente planificadas.
Las resinas también pueden ensayarse por separado en una serie de condiciones ambientales diferentes, estableciendo sus especificaciones y su idoneidad para el uso.
Estos ensayos consisten normalmente en una masa curada de dimensiones determinadas, expuesta a condiciones controladas durante un período de tiempo determinado. El aspecto, las dimensiones y el peso de la resina pueden medirse antes y después del ensayo para identificar si se ha producido algún cambio.
Además, se pueden determinar las propiedades eléctricas y físicas antes y después del ensayo, que pueden ser genéricas o específicas de la aplicación final.
Recubrimientos conformados
Los recubrimientos conformados también pueden utilizarse para proteger los PCB en una variedad de aplicaciones, asegurando un rendimiento óptimo en las condiciones más duras.
Se trata generalmente de películas delgadas aplicadas en el rango de espesor de película seca de 25-250 micrones, lo que conlleva un aumento mínimo del peso del conjunto. Los revestimientos conformes se ajustan a los contornos de la placa, proporcionando la máxima protección con un mínimo de peso o cambio dimensional de la PCB.
Esta es posiblemente la principal ventaja de los revestimientos conformes sobre las resinas de encapsulado y encapsulado. A menudo los revestimientos son claros, por lo que los componentes revestidos son fáciles de identificar y el revestimiento puede ser fácilmente reelaborado y los componentes reemplazados según sea necesario.
La resistencia química y térmica de los revestimientos es generalmente buena para exposiciones cortas. Un revestimiento aplica relativamente poca presión sobre los componentes, lo que constituye una ventaja particular cuando un componente tiene clavijas o patas finas.
El entorno más común al que puede someterse un revestimiento son las condiciones atmosféricas estándar. Por lo general, se realizan pruebas iniciales para evaluar el rendimiento tanto eléctrico como mecánico de la película curada en los sustratos regidos por cada método de prueba estándar.
Después de esto, el ambiente circundante puede ser alterado para evaluar el rendimiento del revestimiento en condiciones más severas. Tales condiciones pueden incluir niebla salina, alta humedad, alta temperatura y cambios térmicos ya sea como un aumento o disminución gradual de la temperatura o un
choque térmico inmediato. Después de la exposición a esos entornos, el revestimiento puede volver a someterse a pruebas para determinar sus propiedades eléctricas y mecánicas y su idoneidad para diversas aplicaciones.
La mayoría de los revestimientos son sistemas de 1K (un solo componente), que tienen una larga vida útil, una baja temperatura de curado o secado y un corto tiempo de secado. Al ser una solución de un solo componente, son claramente más fáciles de procesar y aplicar. Sin embargo, la mayoría de los revestimientos 1K tienen una base de disolvente para modificar su viscosidad a efectos de aplicación.
Los revestimientos pueden aplicarse manualmente con una brocha, una pistola de pulverización o incluso por inmersión manual. Sin embargo, cada vez más, los revestimientos se aplican mediante sistemas robóticos de revestimiento selectivo para proporcionar un proceso más controlado y más consistente.
Por otra parte, los revestimientos de poliuretano de dos partes (2K) recientemente lanzados al mercado combinan la protección y las propiedades de una resina (véase más abajo), con la facilidad de aplicación de un revestimiento de conformidad pero sin el uso de disolventes, lo que les confiere una ventaja medioambiental
Estos pueden proporcionar una excelente cobertura y su flexibilidad superior ofrece protección a los componentes delicados. Los revestimientos 2K también ofrecen excelentes propiedades mecánicas y resistencia a la abrasión pero, al ser de dos partes, requieren un equipo de aplicación más sofisticado que los revestimientos 1K y son más difíciles de eliminar, lo que hace muy difícil la reparación de los tableros.
El amplio uso de la aplicación por pulverización de los revestimientos ha hecho que el revestimiento tenga una viscosidad lo suficientemente baja como para permitir la atomización del material durante el proceso de pulverización. Esto ha significado tradicionalmente que los revestimientos han contenido altos niveles de disolventes para reducir la viscosidad de la resina base.
El contenido de disolventes de muchos revestimientos ha significado que a menudo se utiliza el calor para expulsar los disolventes y permitir que los revestimientos se curen, ya que si se deja curar a temperatura ambiente, el disolvente puede quedar atrapado en el revestimiento causando un fallo prematuro.
Con el aumento de la conciencia ambiental, los tipos de disolventes utilizados han cambiado para reducir los COV (compuestos orgánicos volátiles), así como el porcentaje de disolvente contenido en el revestimiento.
Los materiales de revestimiento modernos suelen estar libres de disolventes y se conocen como sólidos al 100%, porque todo el material aplicado a la placa de circuito se reticula para producir una película seca de grosor similar a la película aplicada en húmedo.
Estos recubrimientos 100% sólidos pueden curarse por calor, humedad o radiación UV dependiendo de la formulación específica.
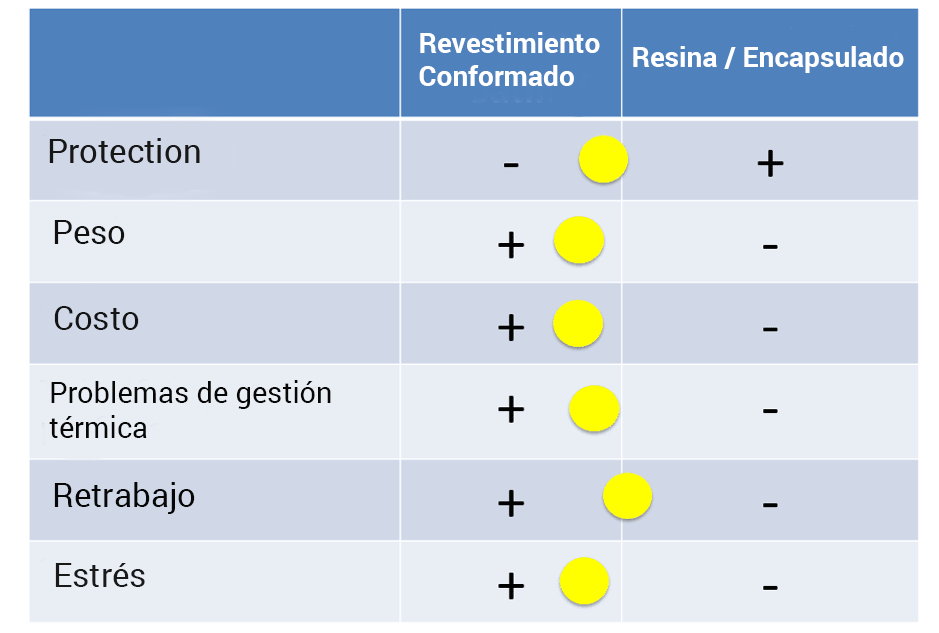
Revestimiento o resina, ¿Cuál elijo?
El diseño del PCB, los componentes utilizados, la carcasa y el entorno de uso final previsto son factores importantes en la decisión de utilizar un revestimiento o una resina.
Como se ha mencionado anteriormente, si la carcasa proporciona una protección primaria adecuada contra el medio ambiente, entonces el uso de un revestimiento puede proporcionar una protección secundaria a la placa en caso de que la protección primaria se dañe o tenga fugas, así como proporcionar protección contra la alta humedad y la condensación dentro de la carcasa.
A menudo se utilizan resinas para formar parte de la propia carcasa y, por lo tanto, forman parte de la protección primaria del sistema, y como tal se requieren para resistir todos los posibles contaminantes y tensiones físicas que la unidad terminada pueda ver durante su entorno de uso final.
Las resinas se utilizan a menudo en la electrónica de alto voltaje y en la electrónica que funciona en ambientes explosivos, para proporcionar una protección total para evitar el arco eléctrico.
Un PCB y una carcasa bien diseñados harán que la aplicación del revestimiento o de la resina sea un proceso rápido y eficiente, eficiente tanto en términos de la cantidad de tiempo necesario para el proceso como de la cantidad de material requerido.
Consultas: Electrical Resin